O společnosti REVOMODS
Evropský výrobce technologicky pokročilých produktů v oblasti modifikace a obnovy třecích povrchů.
Technologie REVOMODS se používá pro všechny kovové třecí povrchy pracující v olejovém prostředí.
Oblast aplikace produktů: spalovací motory, hydraulické systémy, převodovky, rozvodovky, reduktory, kompresory, ložiska všech druhů a další součásti a agregáty.
Naše produkty
- Šetří výrobní a provozní náklady
- Prodlužují životnost a provozní dobu zařízení
- Snižují spotřebu paliva
- Zvyšují energetickou účinnost a účinnost zařízení
- Snižují spotřebu maziv
- Zlepšují ekologičnost zařízení
Oblasti využití
Pro rychlý přechod klikněte na sekci.
- Střední a těžká pozemní technika
- Nákladní doprava
- Stavební a speciální technika
- Rypadla, buldozery a traktory
- Zemědělská technika
- Těžební technika
- Výrobní zařízení
- Dieselové a plynové generátory
- Pohonné jednotky námořní a říční techniky
- Osobní automobily
- Palivová aditiva
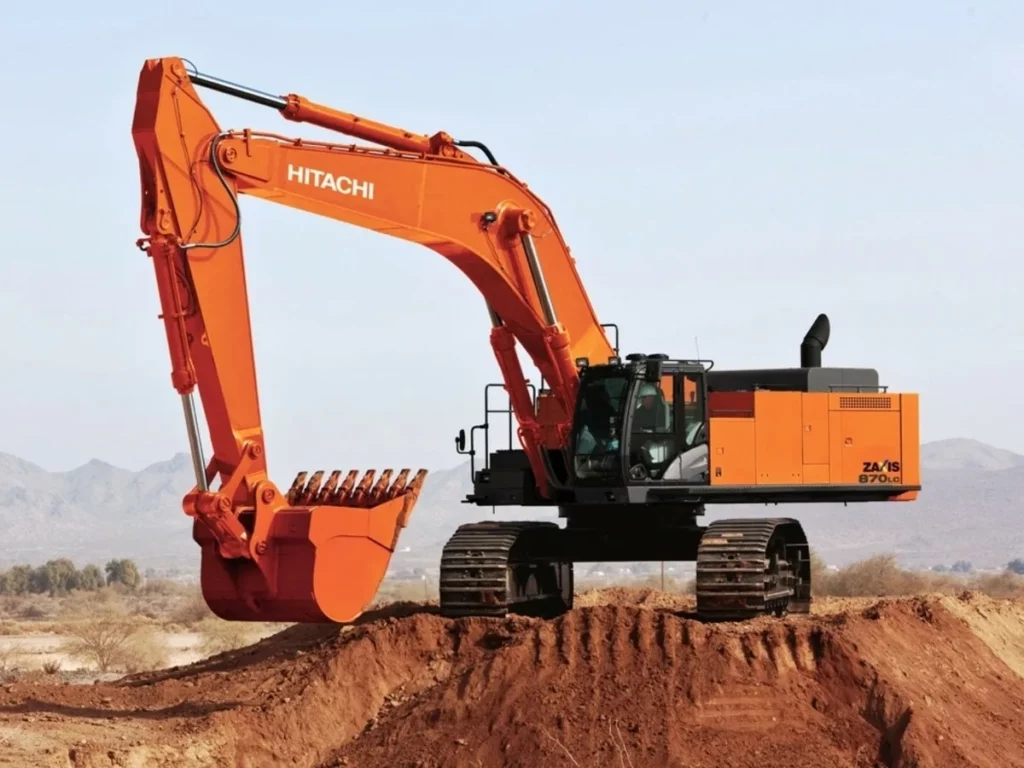
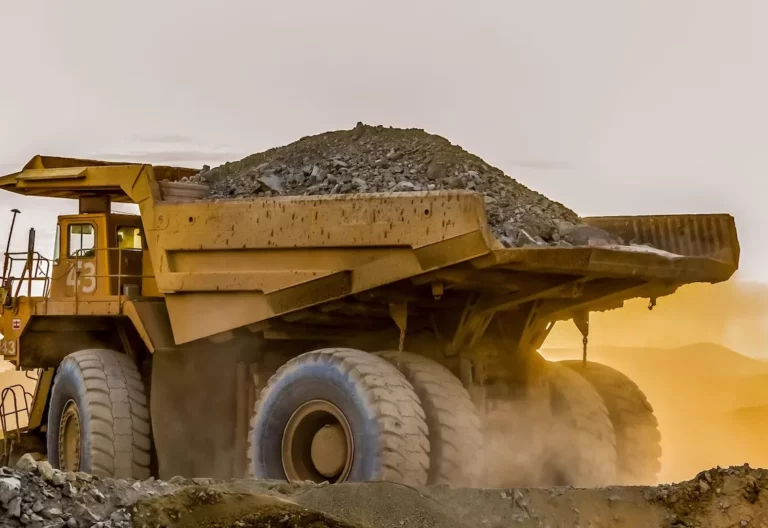
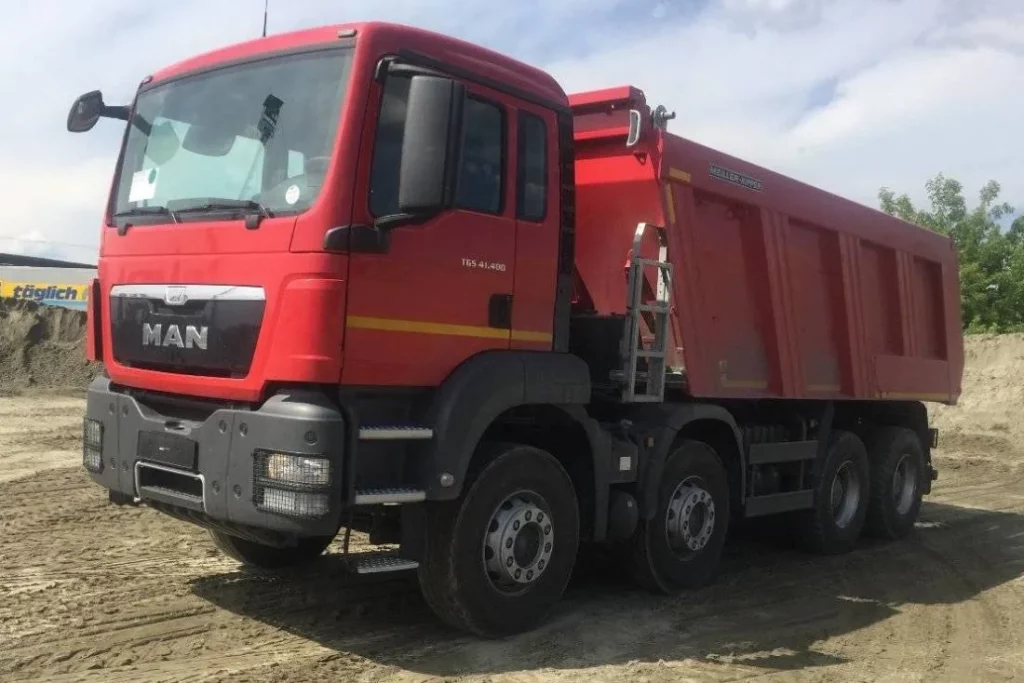
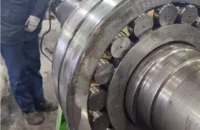
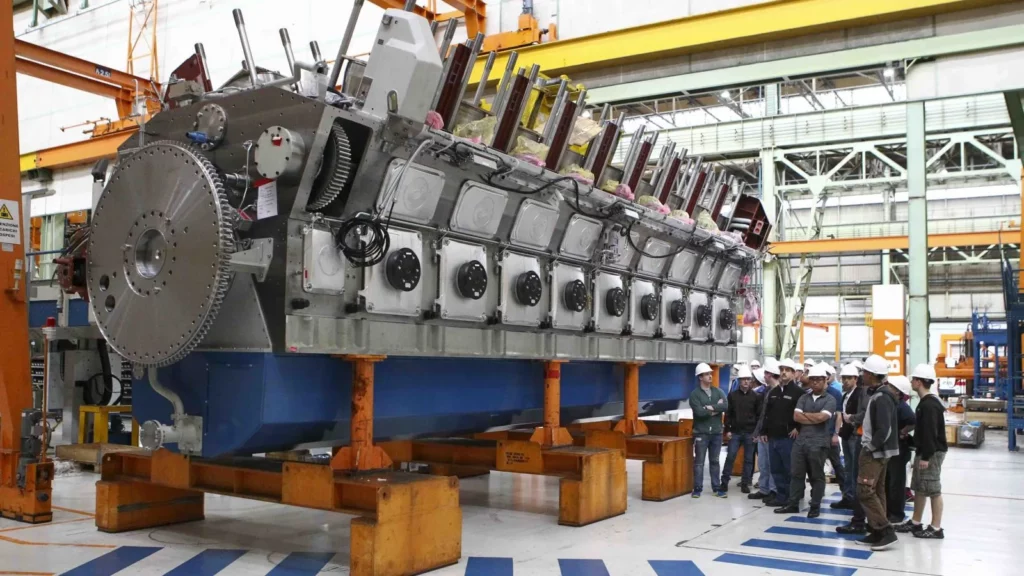
Střední a těžká pozemní technika
Oblasti použití technologie MOTP REVOMODS
- Motory
- Hydraulické systémy
- Mechanické převodovky
- Rozvodovky
- Reduktory
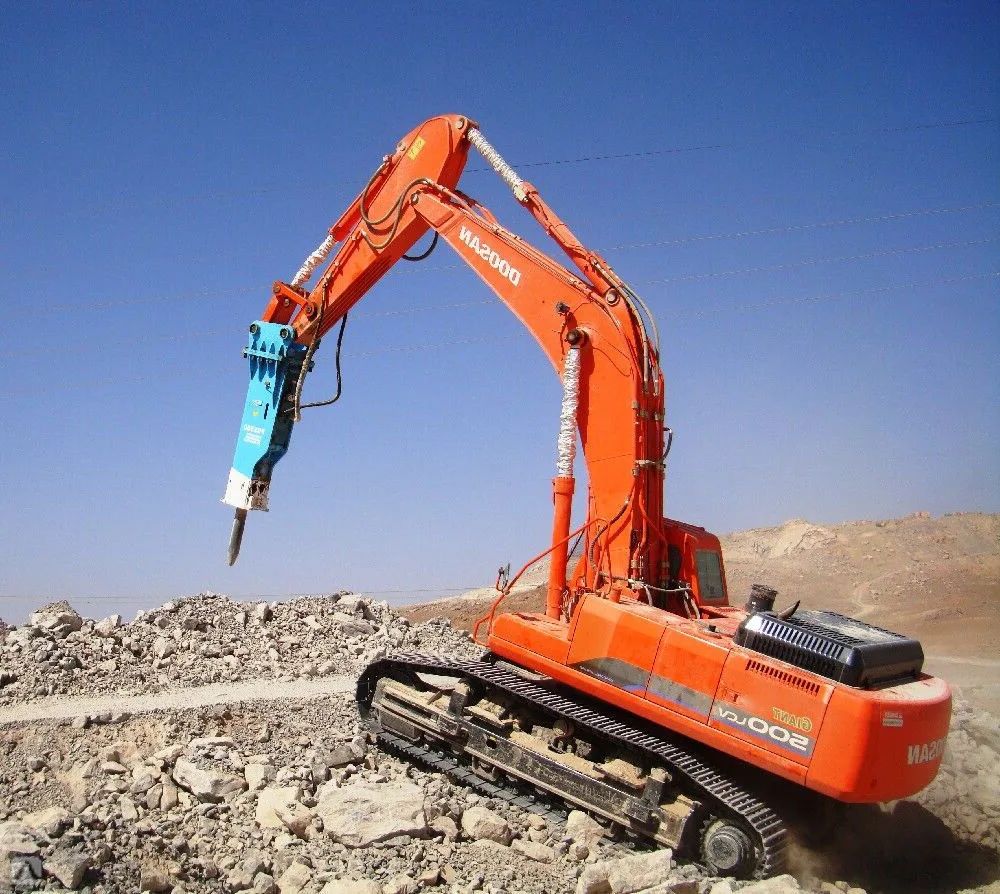
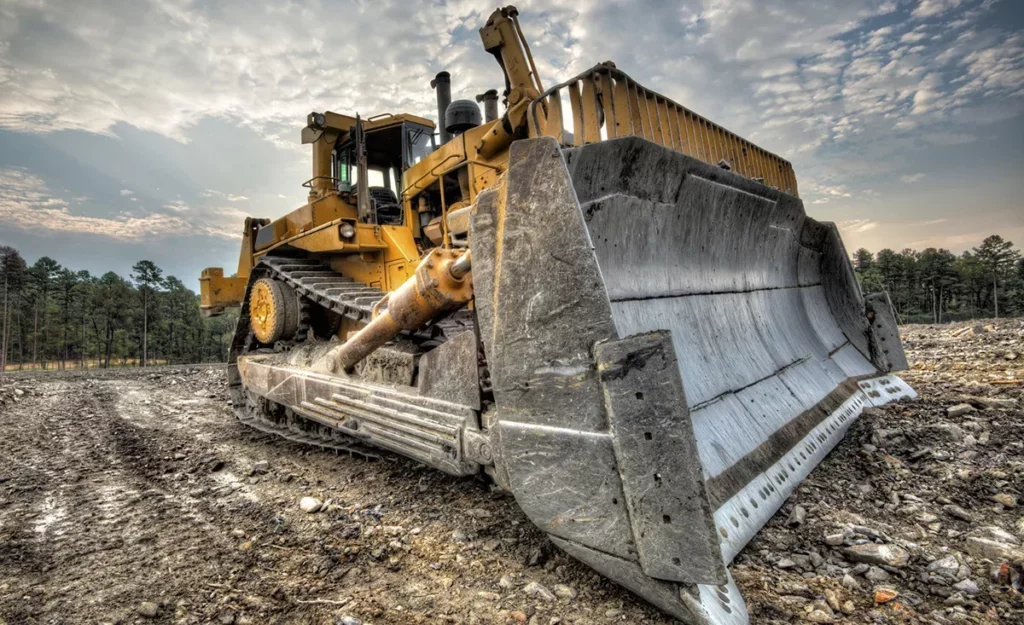
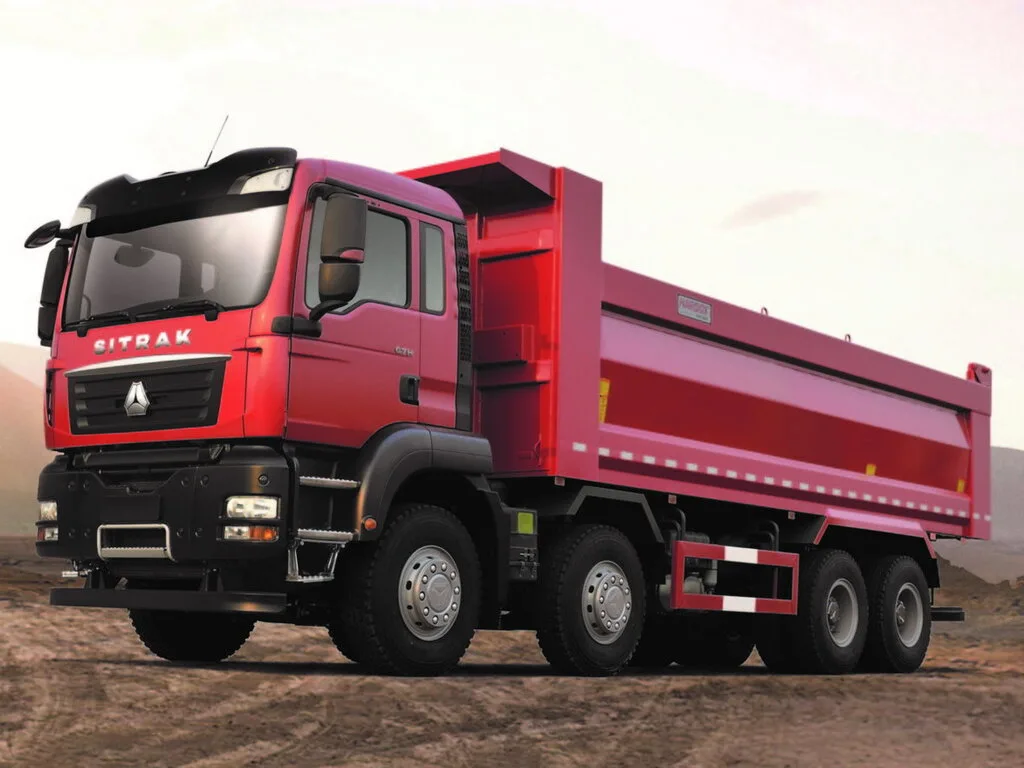
Spalovací motory
Výsledek použití technologie REVOMODS v praxi
- Úspora maziv mezi výměnami oleje až o 99 %
- Snížení spotřeby paliva o 6-22 %
- Prodloužení životnosti motoru o 70-300 %
- Zvýšení účinnosti motoru o 4-12 %
- Úspory na odstávkách a nákladech na opravy
- Snížení škodlivých emisí výfukových plynů o 21-58 %
- Snížení hlučnosti zařízení o 3-9 dB
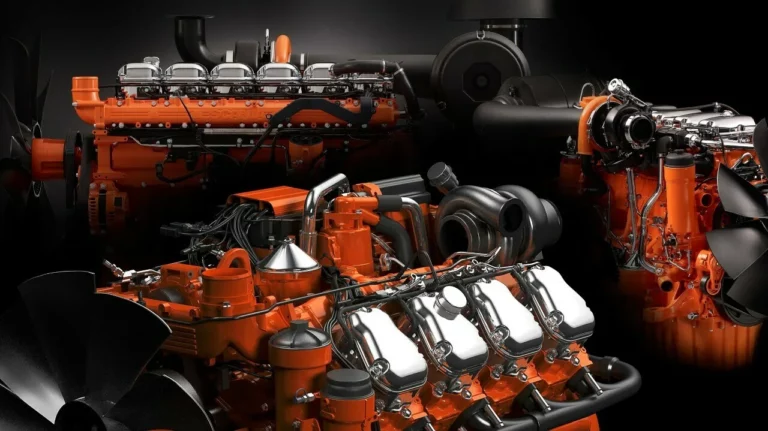
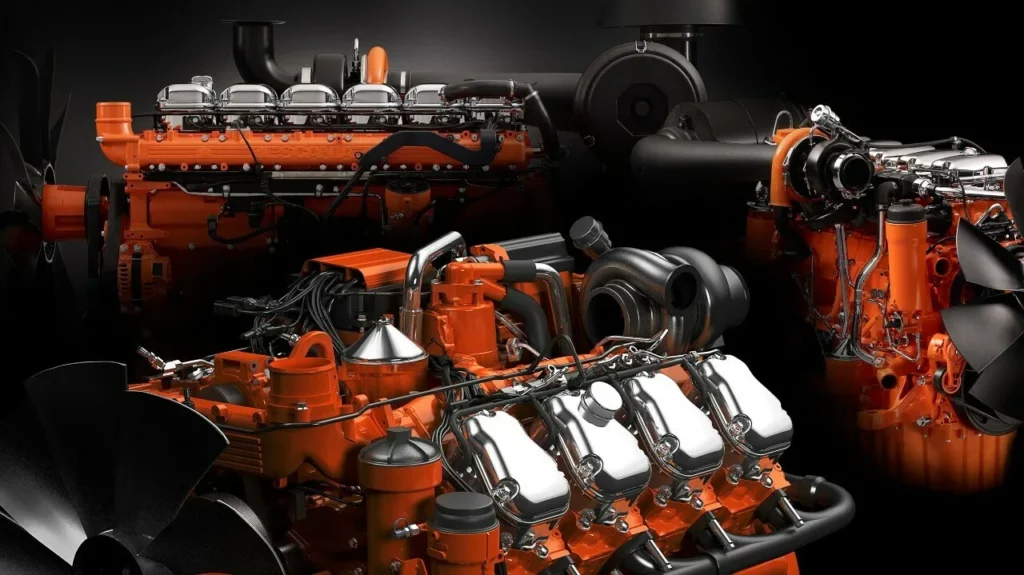
Spotřeba paliva před a po opracování MOTP REVOMODS na nákladním voze MAN 8x8
Vysoce zatížená technika ve stavebním podniku.
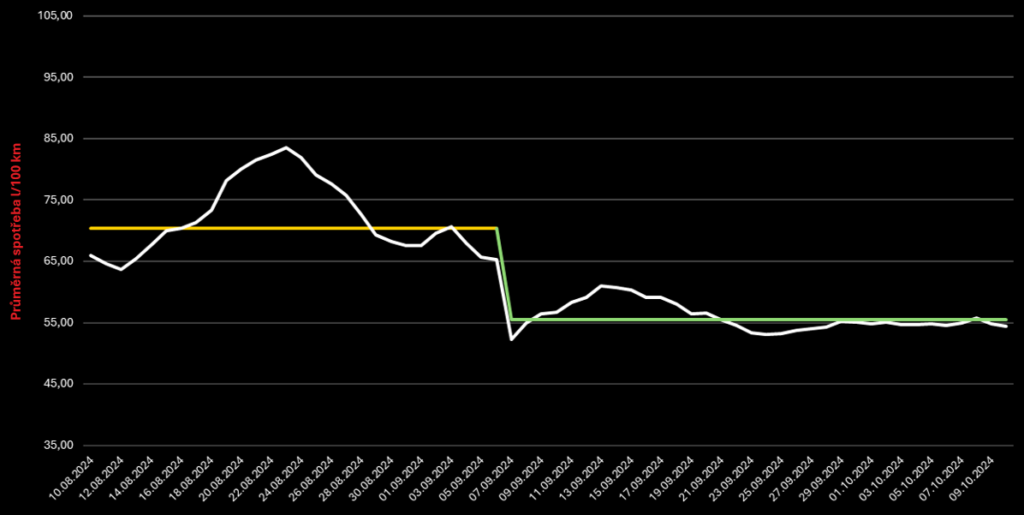
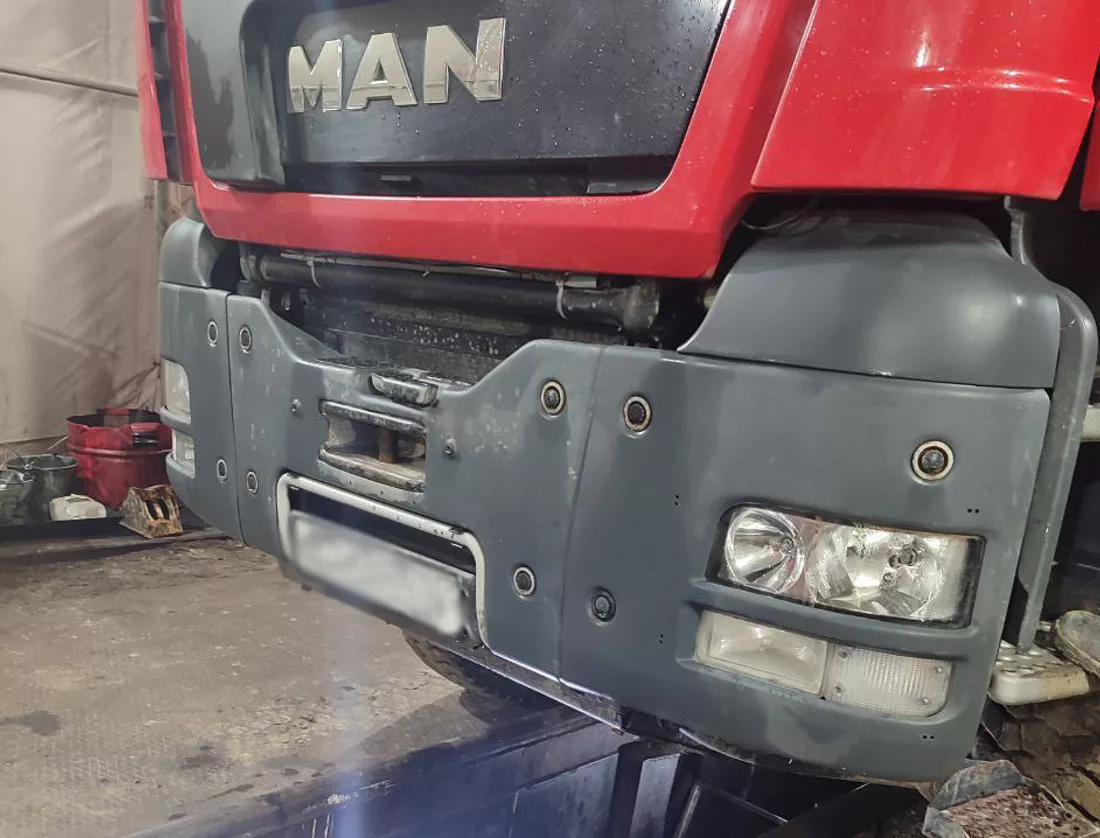
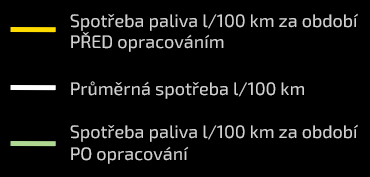
Hydraulické systémy
Výsledek použití technologie REVOMODS v praxi
- Zvýšení životnosti hydraulického čerpadla
- Zvýšení životnosti komponent řízení
- Obnovení tlaku v hydraulickém systému na jmenovitou hodnotu
- Oprava bez rozebrání a odstávky techniky
- Žádný vliv na distribuční zařízení
- Nulová abrazivnost produktu
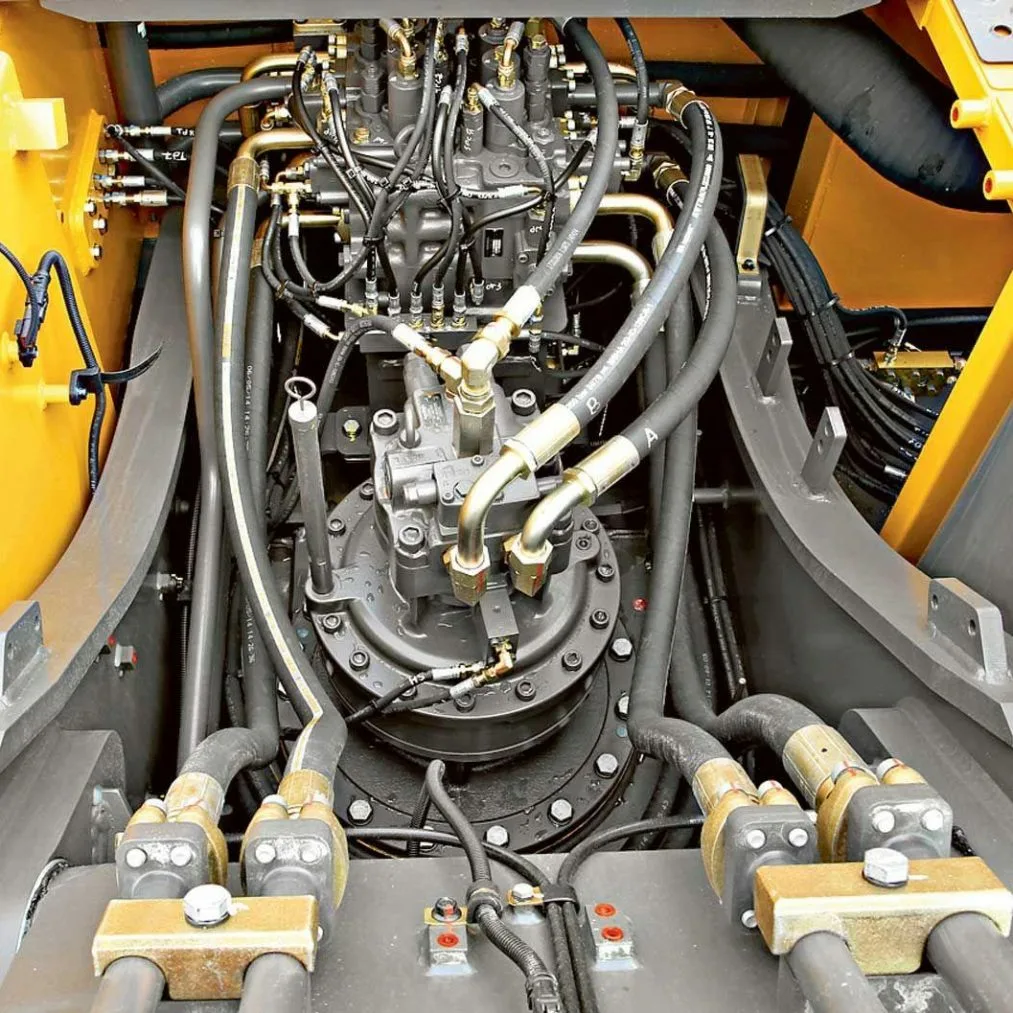
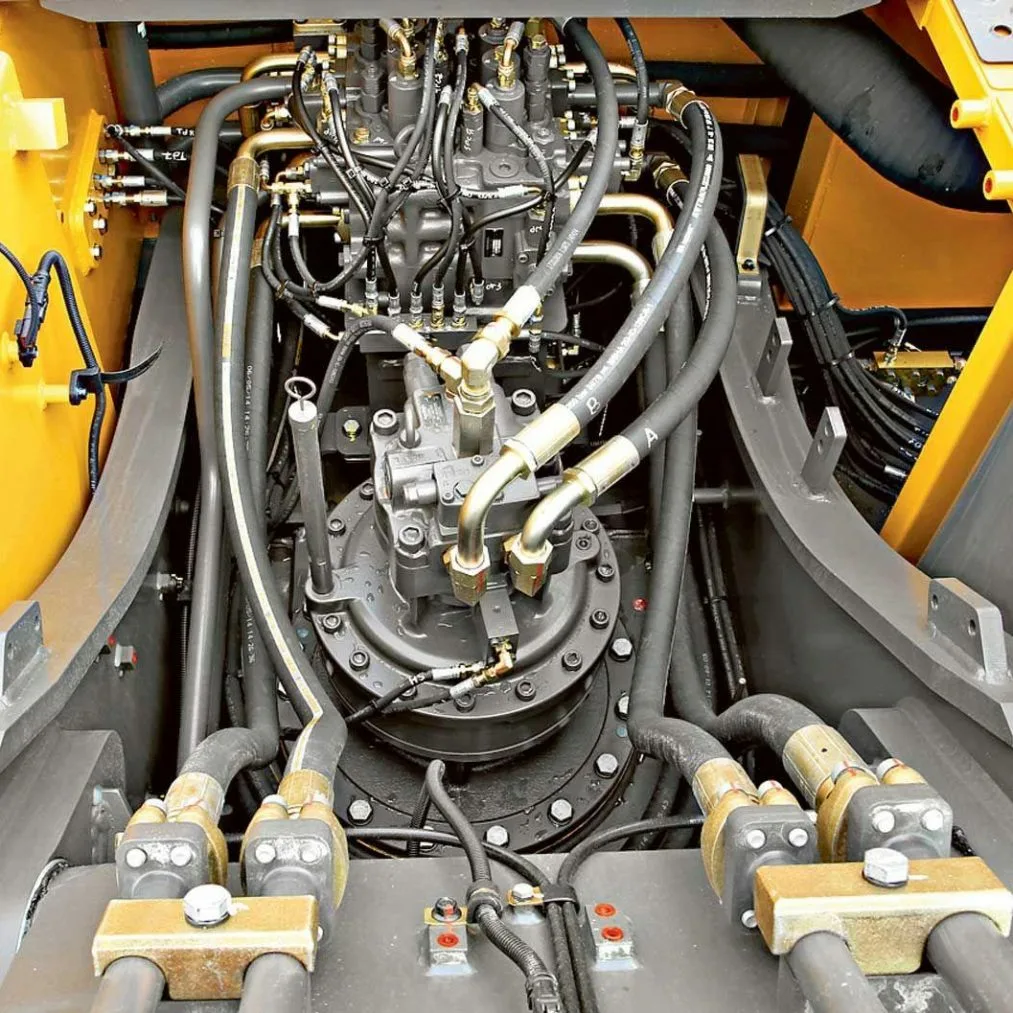
Mechanické převodovky, rozvodovky a reduktory
Výsledek použití technologie REVOMODS v praxi
- Zvýšení celkové životnosti agregátů o 1,5-2násobek
- Zvýšení pevnostní rezervy
- Zvýšení životnosti vnitřních ložisek o 1,5-5násobek
- Zlepšení práce synchronizátorů
- Snížení hlučnosti zařízení o 3-9 dB
- Vymezení vůlí
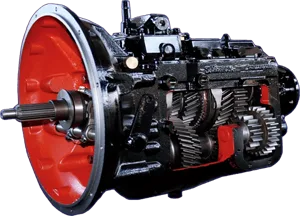
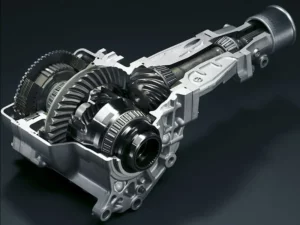
Výrobní zařízení
Oblasti použití technologie MOTP REVOMODS
- Obráběcí stroje
- Hydraulické systémy
- Reduktory a převodovky
- Kompresory
- Chladicí kapaliny
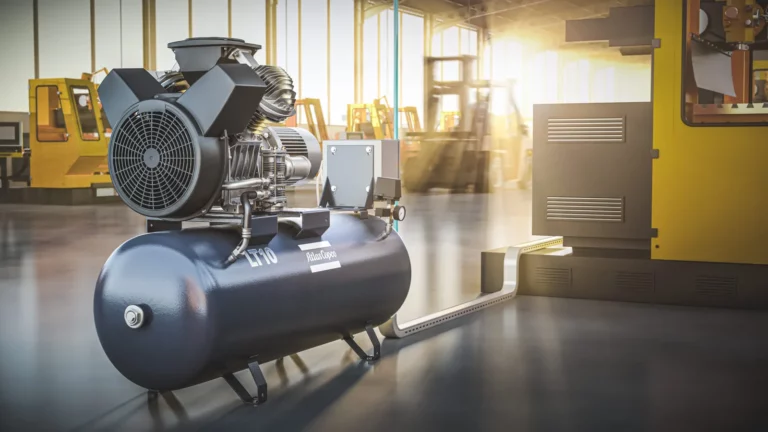
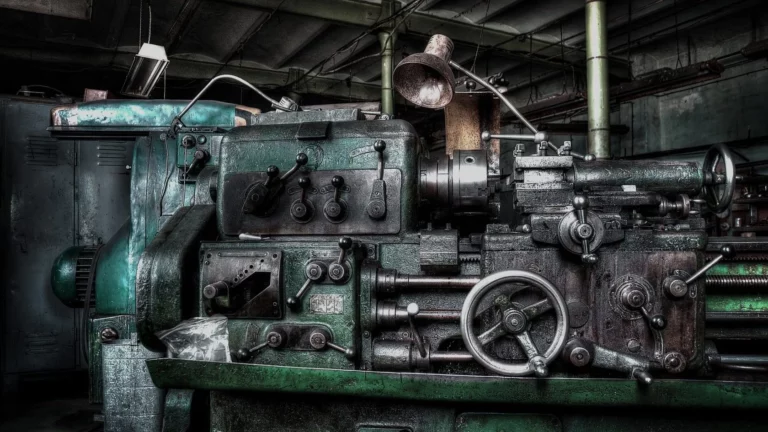
Obráběcí stroje
Výsledek použití technologie REVOMODS v praxi
- Snížení doby odstávek kvůli opravám zařízení
- Zlepšení kvality a přesnosti vyráběných produktů
- Zvýšení energetické účinnosti o 5-16 %
- Prodloužení životnosti ložisek o 1,5-5násobek
- Prodloužení životnosti ozubených kol a hřídelů o 50-300 %
- Vymezení vůlí
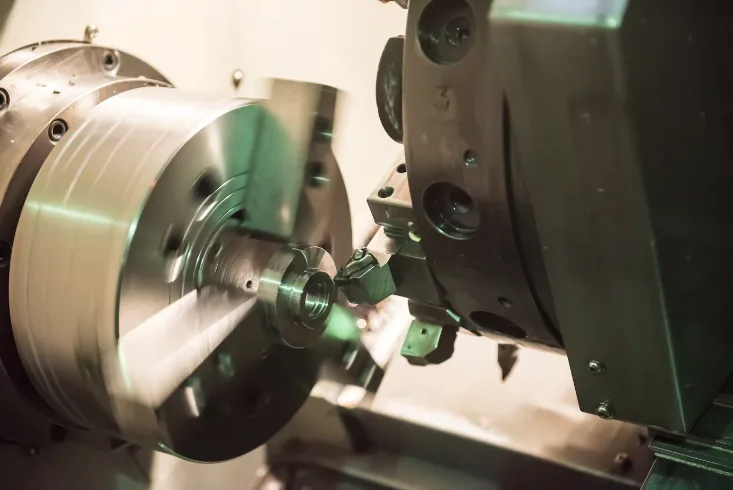
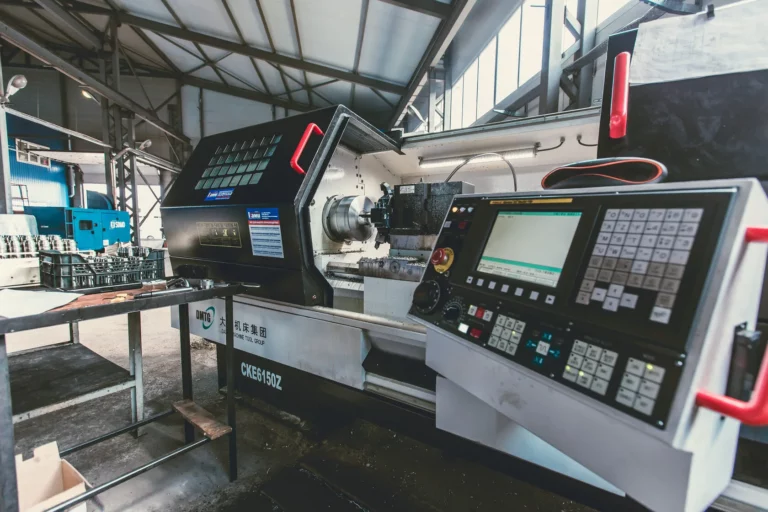
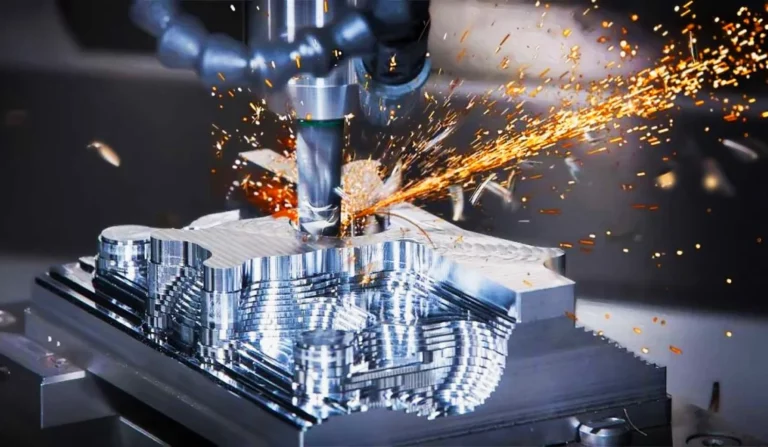
Hydraulické systémy
Výsledek použití technologie REVOMODS v praxi
- Zvýšení životnosti hydraulického čerpadla
- Zvýšení životnosti komponent hydraulického systému
- Obnovení tlaku v systému na jmenovitou hodnotu
- Oprava bez rozebrání a odstávek techniky
- Žádný vliv na distribuční zařízení
- Nulová abrazivnost produktu
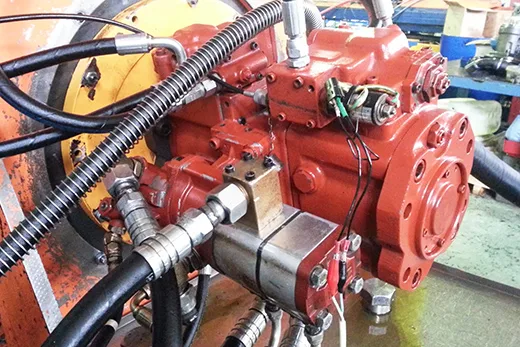
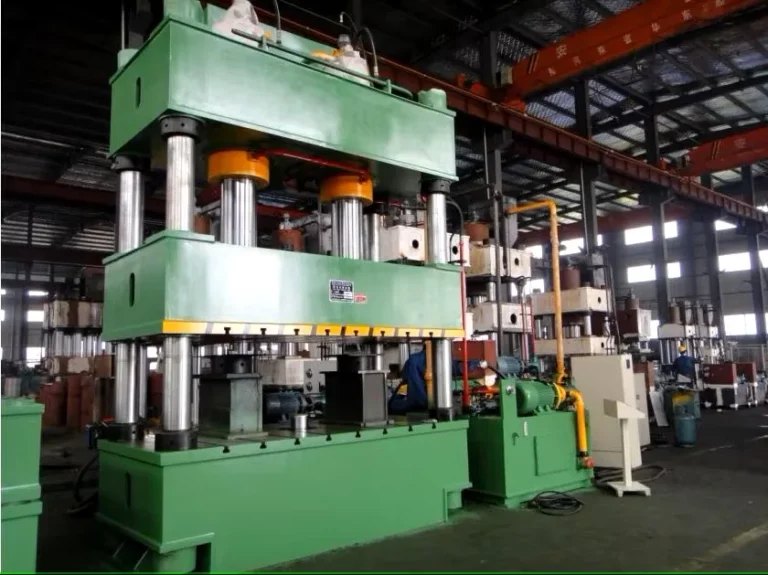
Reduktory, převodovky a kompresory
Výsledek použití technologie REVOMODS v praxi
- Zvýšení celkové životnosti agregátu o 1,5-2násobek
- Zvýšení pevnostní rezervy
- Zvýšení životnosti vnitřních ložisek o 1,5-5násobek
- Zvýšení styčné plochy ozubených převodů
- Vymezení vůlí
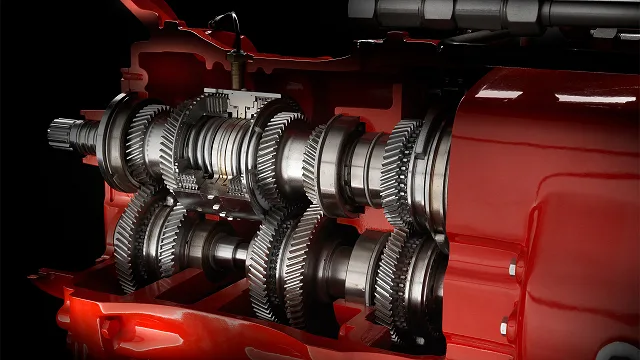
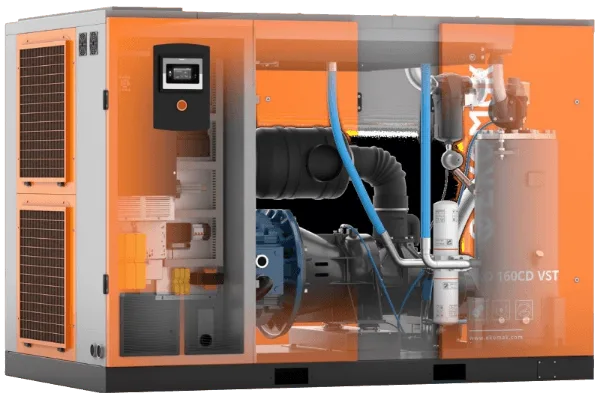
Dieselové a plynové generátory
Výsledek použití technologie REVOMODS v praxi
- Úspora maziv mezi výměnami oleje až o 99 %
- Snížení spotřeby paliva o 6-22 %
- Prodloužení životnosti instalací o 70-300 %
- Zvýšení účinnosti instalace o 4-12 %
- Úspory na odstávkách a nákladech na opravy
- Snížení škodlivých emisí výfukových plynů o 21-58 %
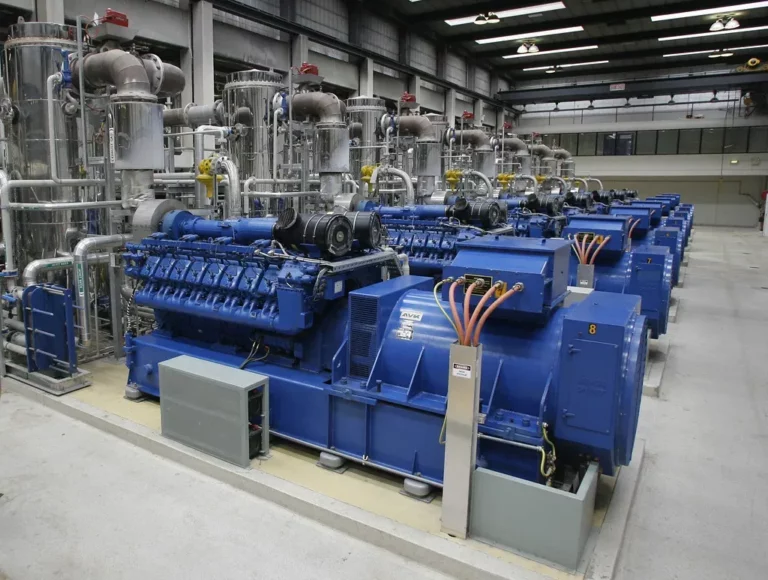
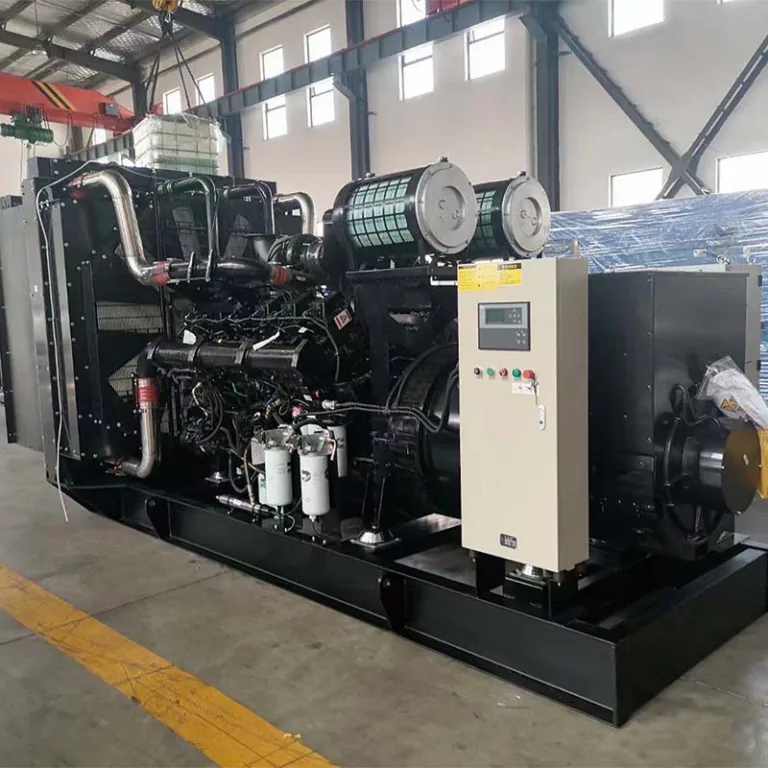
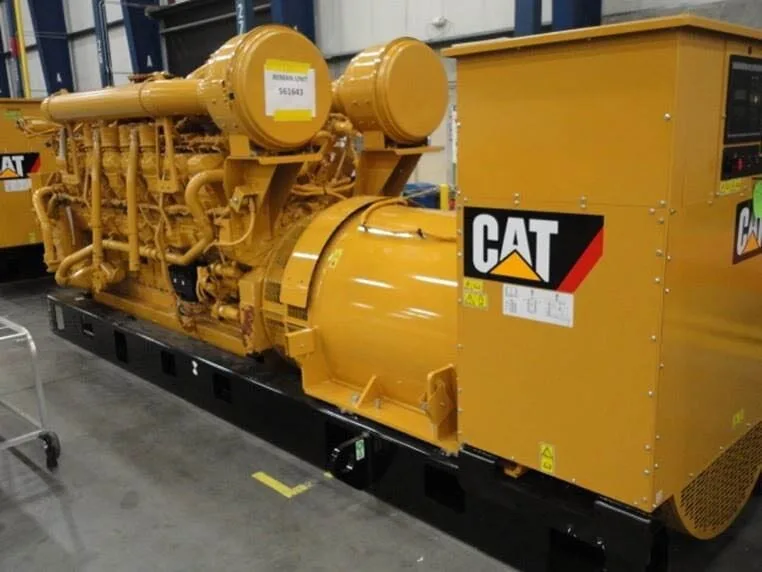
Pohonné jednotky námořní a říční techniky
Výsledek použití technologie REVOMODS v praxi
- Snížení spotřeby paliva o 5-14 % (snížení indexu palivové spotřeby)
- Snížení spotřeby oleje o 35-55 %
- Zvýšení účinnosti hlavního motoru o 4-12 % (snížení mechanických ztrát)
- Zvýšení výkonové rezervy hlavního motoru o 10-35 %
- Snížení škodlivých emisí výfukových plynů o 20-60 %
- Snížení otáček plynových turbín při stejném zatížení
- Prodloužení životnosti hlavního motoru a dieselgenerátorů o 70-300 % (v závislosti na stupni opotřebení v době použití)
- Snížení opotřebení pouzder a vymezení jejich vůlí
- Snížení frekvence odstávek kvůli opravám
Opracované objekty na plavidlech
Hlavní motor (HM)
Palivová zařízení (PZ)
Dieselgenerátor (DG)
Pomocné dieselgenerátory (PDG)
Reduktory
Hydraulické systémy
Ložiska
A další
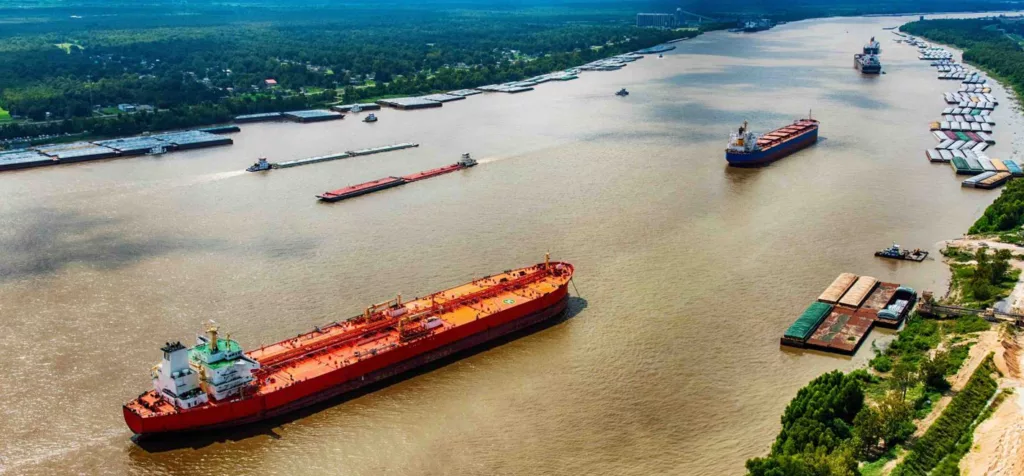
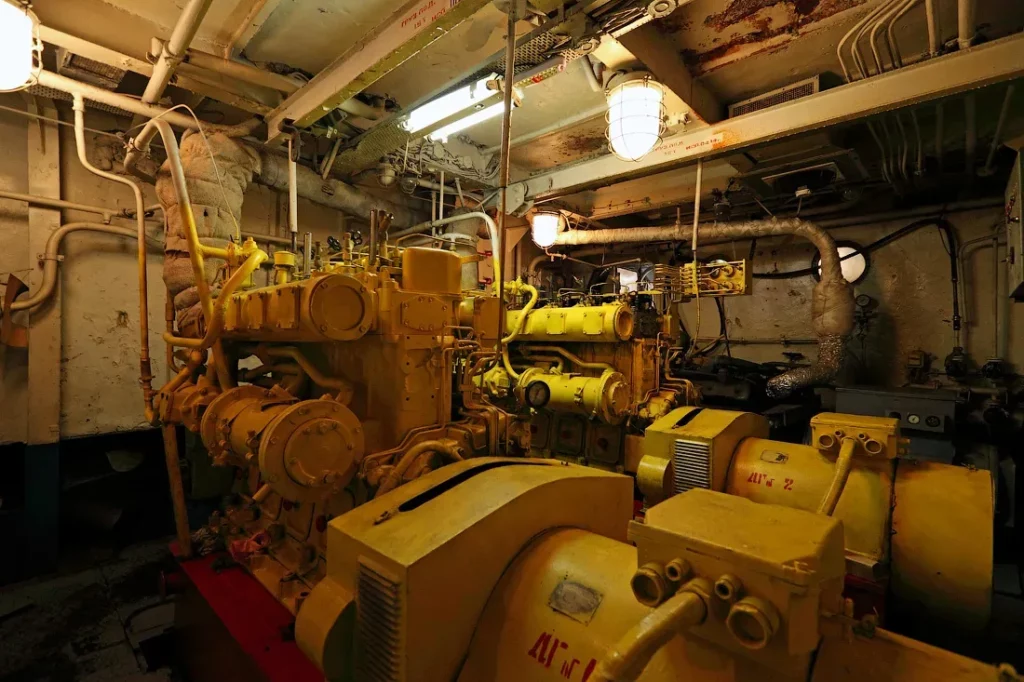
Osobní automobily
Oblasti použití technologie MOTP REVOMODS
- Motory
- Mechanické převodovky
- Rozvodovky
- Reduktory
- Řízení s posilovačem
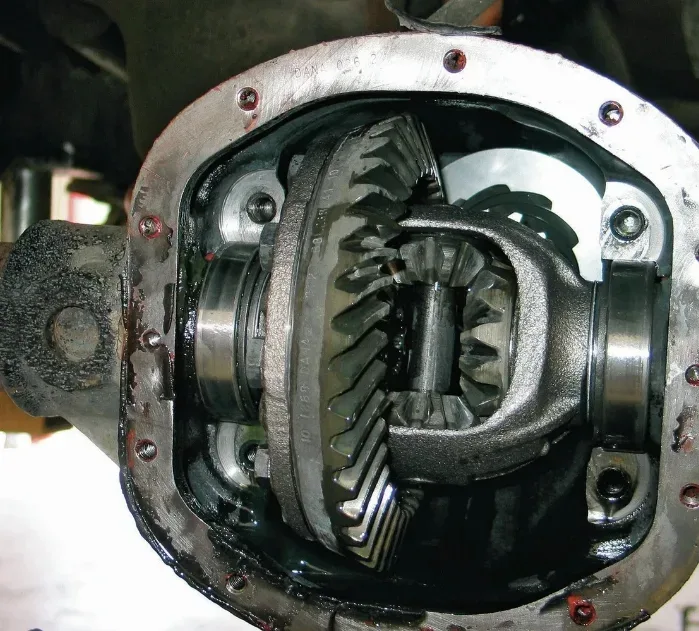
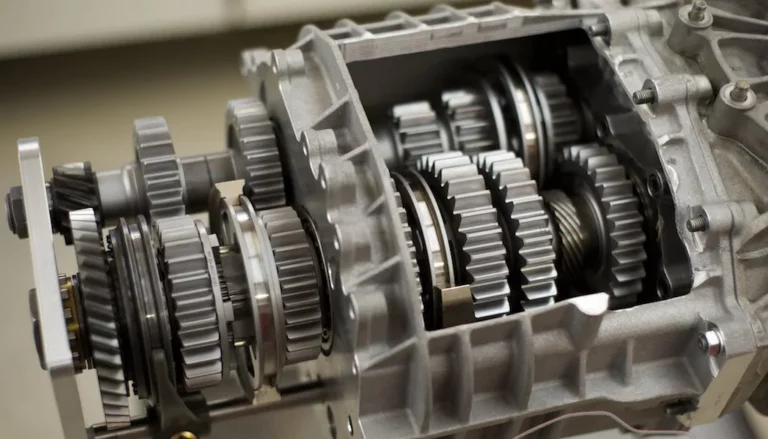
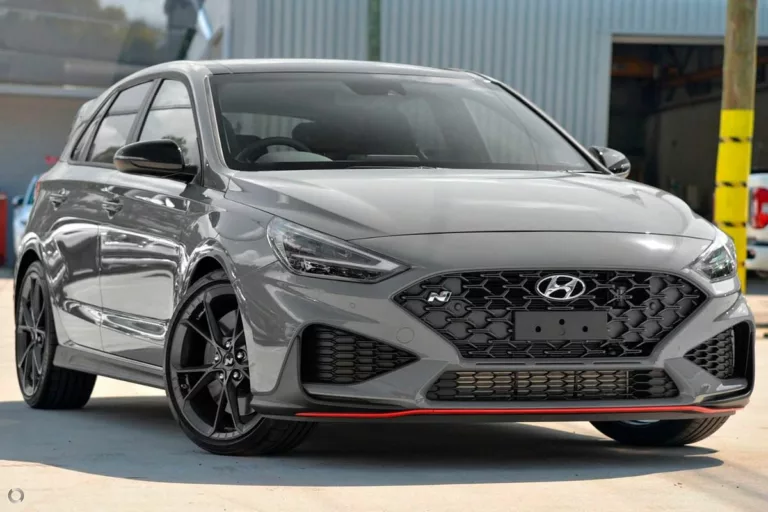
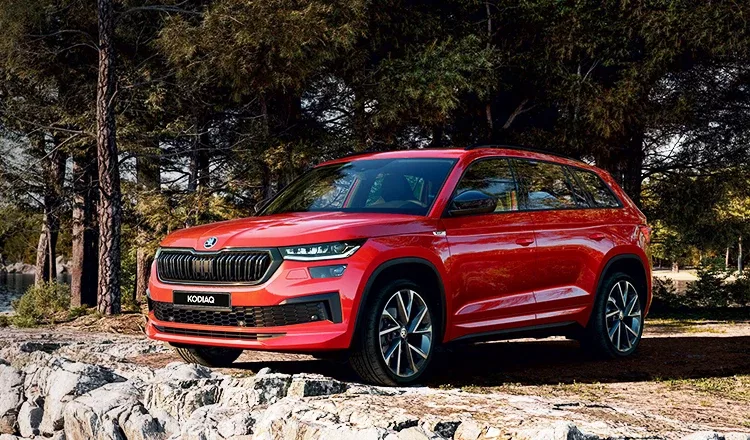
Spalovací motory
Výsledek použití technologie REVOMODS v praxi
- Úspora maziv mezi výměnami oleje až o 99 %
- Snížení spotřeby paliva o 5-14 %
- Snížení škodlivých emisí výfukových plynů o 21-58 %
- Prodloužení životnosti motoru o 70-300 %
- Zvýšení účinnosti motoru o 4-12 %
- Snadné studené starty
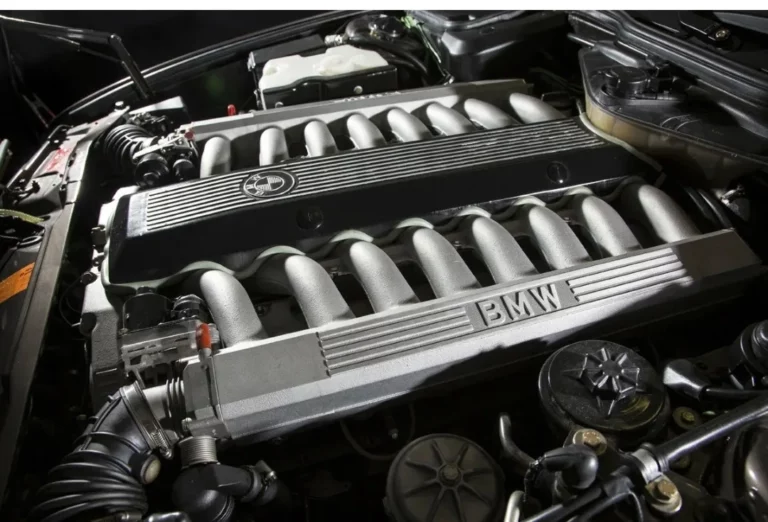
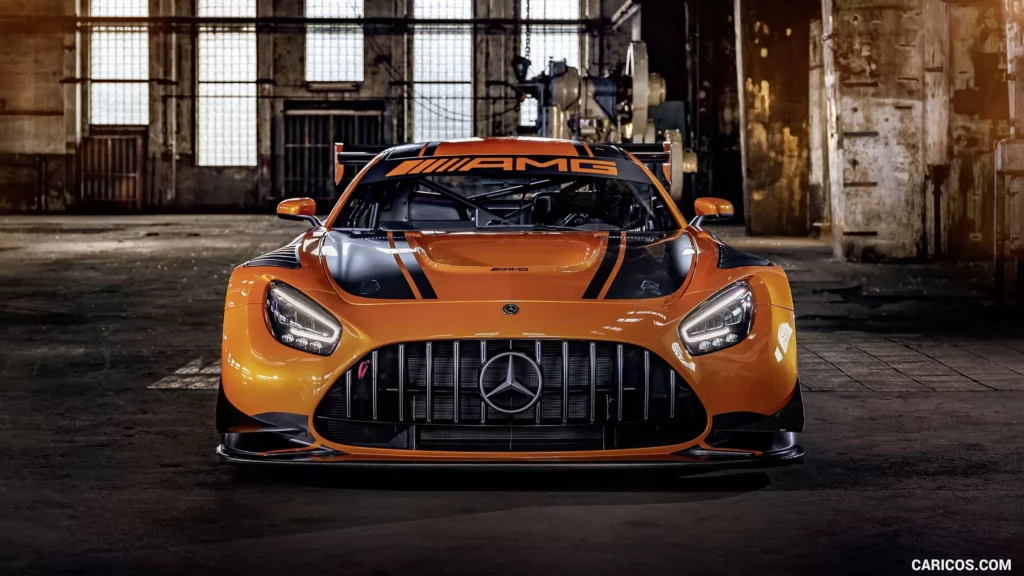
Mechanické převodovky, rozvodovky a reduktory
Výsledek použití technologie REVOMODS v praxi
- Zvýšení celkové životnosti agregátu o 1,5-2násobek
- Zvýšení pevnostní rezervy
- Zvýšení životnosti vnitřních ložisek o 1,5-5násobek
- Zlepšení práce synchronizátorů
- Snížení mechanických ztrát
- Vymezení vůlí
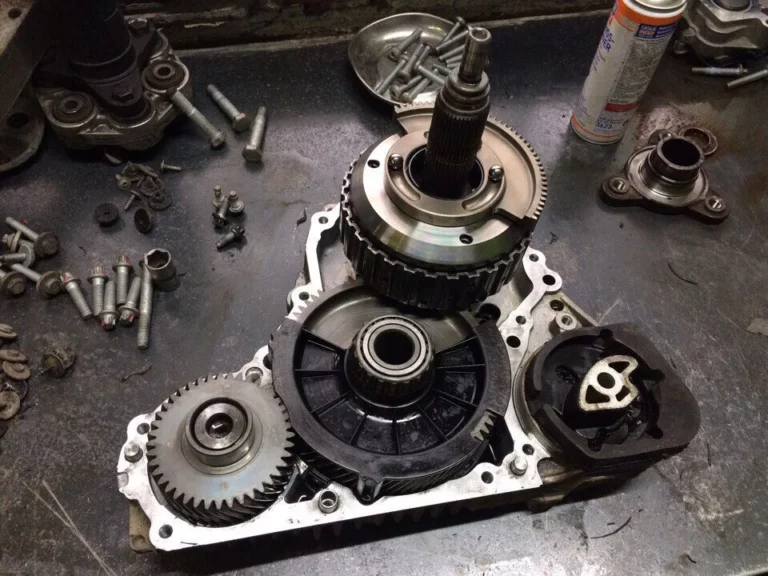
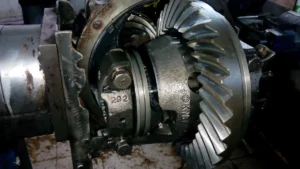
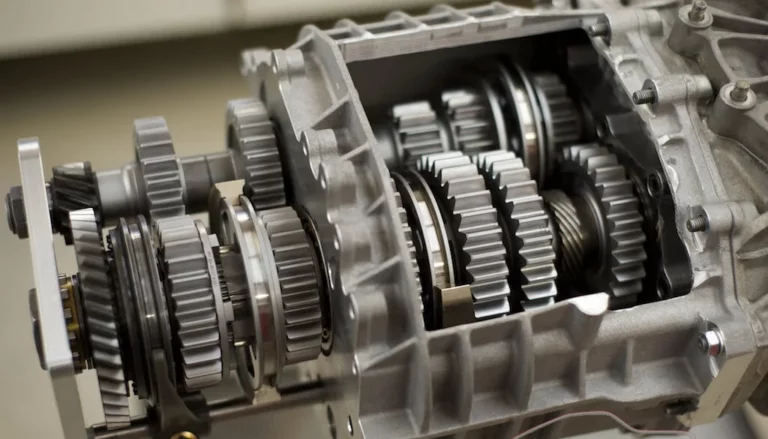
Palivová aditiva
Výsledek použití technologie REVOMODS v praxi
- Zlepšení úplnosti spalování paliva
- Zvýšení točivého momentu motoru
- Ochrana proti korozi kovových částí motoru
- Čištění spalovací komory paliva
- Snížení spotřeby paliva o 3-8 %
- Zvýšení efektivní účinnosti o 4-11 %
- Snížení škodlivých emisí v průměru o 21 %
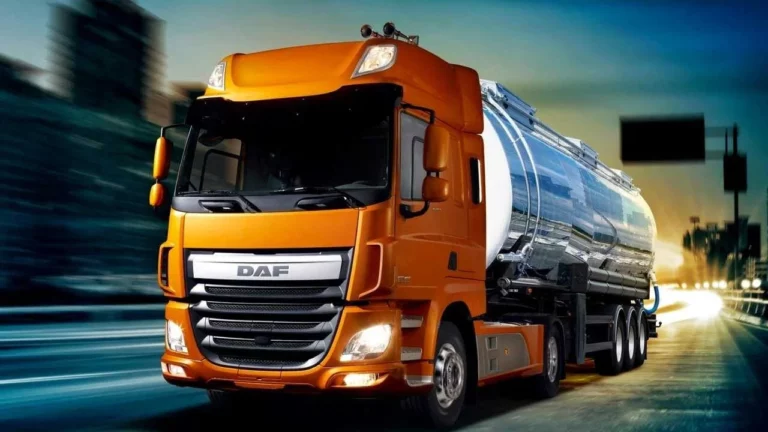
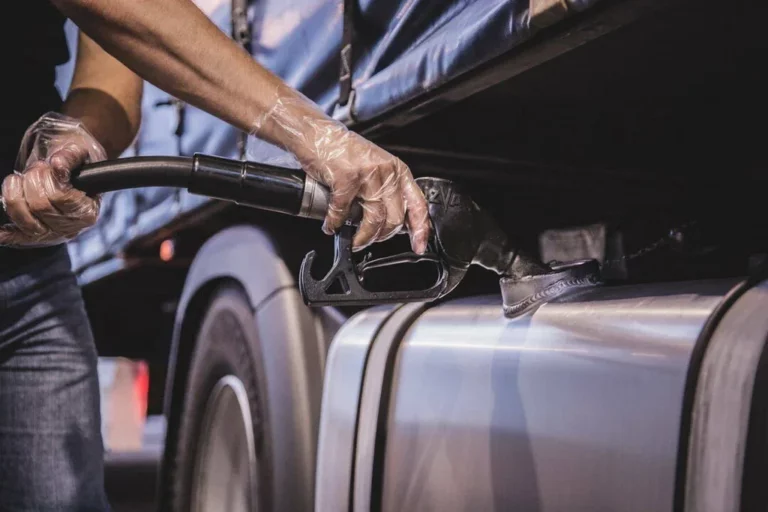
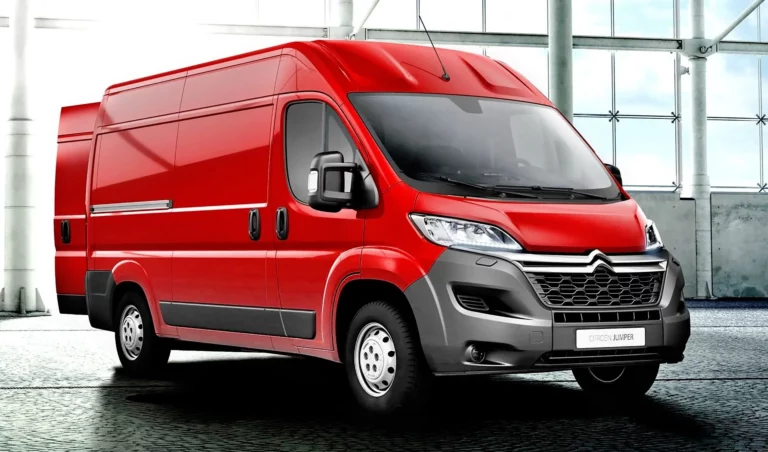